Melbournesparks
Registered

Anyone who builds their own rollingstock has probably run into the problem of how to power it, the lack of cheap and easily available motor blocks has been a huge barrier to entry. To try and solve this problem I've been working on a 3D printable traction motor case that uses cheap and easily obtainable parts, designed so that it can be easily adapted to power just about any 45mm gauge rollingstock. The STL file is now up on Thingiverse for anyone who wants to make their own. The prototype versions have been powering the W class and toast rack tram for quite a number of real kilometers now with good results, on a long and steeply graded line.
45mm gauge traction motor case by Melbournesparks|
Here's ebay links for the motor and gears used. Ebay links are unlikely to stay current forever but you should be able to find equivalent parts by searching:
motor FF-130SH 1pcs FF-130SH DC 12V 4500RPM High Torque Great Torsion Mute Micro Motor for DIY | eBay
gear 1 9T 50PCS X 9T Plastic Spur Gear Teeth=9 Aperture:2mm 0.5 Modulus Accessories 1.95MM | eBay
gear 2 34T+12T 100pcs 34 Teeth Electric Machanical Model Motor Gear Wheel 3412-2B 605322478027 | eBay
gear 3 40t 100PCS 40 Teeth 3mm Hole Diameter Plastic Gear Wheel for RC Car 605322558002 | eBay
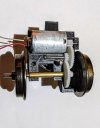
45mm gauge traction motor case by Melbournesparks|
Here's ebay links for the motor and gears used. Ebay links are unlikely to stay current forever but you should be able to find equivalent parts by searching:
motor FF-130SH 1pcs FF-130SH DC 12V 4500RPM High Torque Great Torsion Mute Micro Motor for DIY | eBay
gear 1 9T 50PCS X 9T Plastic Spur Gear Teeth=9 Aperture:2mm 0.5 Modulus Accessories 1.95MM | eBay
gear 2 34T+12T 100pcs 34 Teeth Electric Machanical Model Motor Gear Wheel 3412-2B 605322478027 | eBay
gear 3 40t 100PCS 40 Teeth 3mm Hole Diameter Plastic Gear Wheel for RC Car 605322558002 | eBay
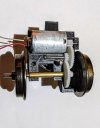