trammayo
Interested in vintage commercial vehicle, trams, t

Last year I acquired a cheapo plastic traction engine (1/24 scale) from ebay. For a plastic toy, the £5 was a bit dear but, for as a starter for a project the price was right.
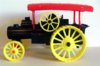
I had it posted to my son`s address so I didn`t get hold of it until long after it was delivered - so I couldn`t really complain about the missing chimney!
Having it in my hands, I could see it had possibilities when I could find time to do something with it.
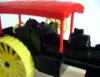
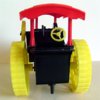
It had moulded-in detailing which I might be able to enhance, plus I could add things - like the steering chains etc.
The most glaring discrepancies - to me - were the flywheel alignment (directly over the back wheel which would foul a drive belt) and the `humpbacked` canopy!
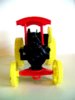
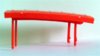
Anyway, yesterday was the time. Inbetween resting (from cutting the grass/moss - daren`t call it a lawn) and other domestiicity, I stripped it down and began pruning the plastic.
The boiler splits in half horizontally and and is held together by lugs and the front smokebox door. This then allowed me to remove a chunk of plastic to allow the flywheel to be moved inboard by about 8mm. On the opposite side, a moulded-in lever obstructed my plans to fit a train of gears so that was hacked away.
I then looked at the rear wheels. On the `drive` side, I removed a portion of the wheel`s boss to all ow the gear wheel to sit in line (with the rest of the gears. Next I thought about clutch and brake drums. These were cut from uPVC fascia board with a hole saw. Next the holes were drilled out to 9.5mm which allowed a tight push fit over the wheel bosses.
I then reassembled the wheels and axle, including the final drive gear. Next, I drilled a hole in line with the drive shaft and shoved in a piece of 2.5mm steel rod to receive the gear pinnion.
Satisfied that it looked OK, I pushed the axle in place and was able to mesh in the intermediate gear and mark where I needed to drill. The shaft was made long enough to push right through to the other side. This imparted some extra strength to compensate for all the plastic that had been removed!
I also removed another moulding which was forward of (what would be) the motion guard plate. I still have some filling to do there. Next I drilled a couple of holes in the cylinders and the plate and shoved some more 2mm steel rod in to represent the piston rods.
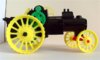
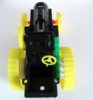
I have temporaly reassembled everything - apart from the canopy - but today it will taken apart, filled where required, and given a coat of plastic primer and an undercoat.
As for the canopy, it was obviously produced with its multiplicity of compound curves as it refused to straighten out with the applied heat of the blowlamp. But, waste not want not, I went out after tea and savagely attacked the edges with a hacksaw. Both sides now have a series of apparently indiscriminate cuts and the canopy has been straightened (I hope permanently). The edges were reinforced with wood strips behind them. I have used ABS glue and loads of mini clamps so I`ll know this morning if it has worked!
to be continued ....
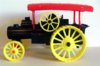
I had it posted to my son`s address so I didn`t get hold of it until long after it was delivered - so I couldn`t really complain about the missing chimney!
Having it in my hands, I could see it had possibilities when I could find time to do something with it.
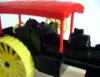
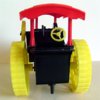
It had moulded-in detailing which I might be able to enhance, plus I could add things - like the steering chains etc.
The most glaring discrepancies - to me - were the flywheel alignment (directly over the back wheel which would foul a drive belt) and the `humpbacked` canopy!
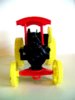
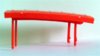
Anyway, yesterday was the time. Inbetween resting (from cutting the grass/moss - daren`t call it a lawn) and other domestiicity, I stripped it down and began pruning the plastic.
The boiler splits in half horizontally and and is held together by lugs and the front smokebox door. This then allowed me to remove a chunk of plastic to allow the flywheel to be moved inboard by about 8mm. On the opposite side, a moulded-in lever obstructed my plans to fit a train of gears so that was hacked away.
I then looked at the rear wheels. On the `drive` side, I removed a portion of the wheel`s boss to all ow the gear wheel to sit in line (with the rest of the gears. Next I thought about clutch and brake drums. These were cut from uPVC fascia board with a hole saw. Next the holes were drilled out to 9.5mm which allowed a tight push fit over the wheel bosses.
I then reassembled the wheels and axle, including the final drive gear. Next, I drilled a hole in line with the drive shaft and shoved in a piece of 2.5mm steel rod to receive the gear pinnion.
Satisfied that it looked OK, I pushed the axle in place and was able to mesh in the intermediate gear and mark where I needed to drill. The shaft was made long enough to push right through to the other side. This imparted some extra strength to compensate for all the plastic that had been removed!
I also removed another moulding which was forward of (what would be) the motion guard plate. I still have some filling to do there. Next I drilled a couple of holes in the cylinders and the plate and shoved some more 2mm steel rod in to represent the piston rods.
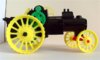
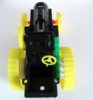
I have temporaly reassembled everything - apart from the canopy - but today it will taken apart, filled where required, and given a coat of plastic primer and an undercoat.
As for the canopy, it was obviously produced with its multiplicity of compound curves as it refused to straighten out with the applied heat of the blowlamp. But, waste not want not, I went out after tea and savagely attacked the edges with a hacksaw. Both sides now have a series of apparently indiscriminate cuts and the canopy has been straightened (I hope permanently). The edges were reinforced with wood strips behind them. I have used ABS glue and loads of mini clamps so I`ll know this morning if it has worked!
to be continued ....