tramcar trev
all manner of mechanical apparatus...
Creating faux granite or stone was my aim in this exercise. My WWI Memorial plinth fell to bits and after a bit of research I decided to go down the road of making my own fake stone. To get real granite cut to size was expensive and the texture would have been over scale. Sand has just the right size for the different colour flecks in the real stuff.
Ok from the benefit of my experience this is how I did the job;
Washed my sands carefully to remove any salts that inhibits the curing of the resin. Modellers tip, keep some strong plastic bags with you at all times so that you can scrounge sand of different colours as you travel around.
Mix some sands of various colours to get the colour you want remembering that once the sand is mixed with resin the colour will intensify. To get an idea of the finished colour wet some of the sand mix.
Measure out the quantity of sand needed to fill the mould either using maths or more practically by filling the mould with sand then tipping it into a measuring jug. Its important to know how much sand will fill the mould.
Then prepare the resin, I used polyester resin because it states clearly on the package that it is both weatherproof and UV resistant. You will need around 1/3 mixed resin to whatever the volume of the sand is; in my case it was 150 ml sand so 50mL of resin makes the mix pourable. So now you ask if the mould takes 150ml of sand and you add 50ml of resin you must have 50ml left over, but I didn’t have that so I’m assuming that there is lots of air between the grains of sand that the resin fills. Mix the resin with its hardener slowly, lets not agitate it too much you DO NOT want too much air in it.
Slowly fold the sand into the resin, once again trying to avoid the inclusion of air... DO NOT do it the other way around and pour the resin onto the sand. If you find the mix too stiff add more resin/hardener mix. If you have too much resin the sand will sink to the bottom leaving a band of clear resin at the top.
Pour the mix into your prepared mould slowly and try and tap or vibrate the mould to get any excess air to the surface and allow to cure.
Demould and allow to cure off the excess MEKP, best done outside in the sun and rain for as long as possible (7days) before sticking anything to the job....
I haven`t described making the mould, we have done that before but I should give a warning re the Polyester Resin. The hardener (catalyst), Methyl Ethyl Keytone Peroxide is really dangerous stuff so its best to work using disposable gloves and some form of eye protection are the basic necessities for safety. Of course you could use Epoxy Resin.............
I shall be able to make “sheets” of roof tiles and bricks using this technique with either terracotta coloured sand from Peterborough and deep red sand from Alice Springs (Bricks can be any earthy colour) and pressing chopped strand fibreglass cloth into the back of it.
The dark red granite I made looks quite convincing and bears a striking resemblance to the Granite used to create the Devils Marbles and Murphy’s Haystacks....
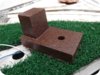
Ok from the benefit of my experience this is how I did the job;
Washed my sands carefully to remove any salts that inhibits the curing of the resin. Modellers tip, keep some strong plastic bags with you at all times so that you can scrounge sand of different colours as you travel around.
Mix some sands of various colours to get the colour you want remembering that once the sand is mixed with resin the colour will intensify. To get an idea of the finished colour wet some of the sand mix.
Measure out the quantity of sand needed to fill the mould either using maths or more practically by filling the mould with sand then tipping it into a measuring jug. Its important to know how much sand will fill the mould.
Then prepare the resin, I used polyester resin because it states clearly on the package that it is both weatherproof and UV resistant. You will need around 1/3 mixed resin to whatever the volume of the sand is; in my case it was 150 ml sand so 50mL of resin makes the mix pourable. So now you ask if the mould takes 150ml of sand and you add 50ml of resin you must have 50ml left over, but I didn’t have that so I’m assuming that there is lots of air between the grains of sand that the resin fills. Mix the resin with its hardener slowly, lets not agitate it too much you DO NOT want too much air in it.
Slowly fold the sand into the resin, once again trying to avoid the inclusion of air... DO NOT do it the other way around and pour the resin onto the sand. If you find the mix too stiff add more resin/hardener mix. If you have too much resin the sand will sink to the bottom leaving a band of clear resin at the top.
Pour the mix into your prepared mould slowly and try and tap or vibrate the mould to get any excess air to the surface and allow to cure.
Demould and allow to cure off the excess MEKP, best done outside in the sun and rain for as long as possible (7days) before sticking anything to the job....
I haven`t described making the mould, we have done that before but I should give a warning re the Polyester Resin. The hardener (catalyst), Methyl Ethyl Keytone Peroxide is really dangerous stuff so its best to work using disposable gloves and some form of eye protection are the basic necessities for safety. Of course you could use Epoxy Resin.............
I shall be able to make “sheets” of roof tiles and bricks using this technique with either terracotta coloured sand from Peterborough and deep red sand from Alice Springs (Bricks can be any earthy colour) and pressing chopped strand fibreglass cloth into the back of it.
The dark red granite I made looks quite convincing and bears a striking resemblance to the Granite used to create the Devils Marbles and Murphy’s Haystacks....
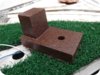