idlemarvel
Neither idle nor a marvel

This is how I converted an old model LGB 2095 to DCC. This is a long posting and should only be read if you want to actually do the same thing or you have plenty of time on your hands!
This model had old power blocks with only two external connections (track power). DCC requires you to intercept the track power before distributing it to the motors. The power connection from the track to the motor is handled inside the block so you have to dismantle the two power blocks and get the soldering iron out.
As I have never dismantled a power block before I did a bit of googling and I found this YouTube video from a chap called Bam Bam very helpful:
Although it is for a Stainz the power block is the same.
It also had two handy tips that apply to any work like this:
1 – Always try out your newly wired decoder on programming track first. If you can’t read or write a CV something is wrong, most likely a short somewhere. If you connected this straight to power you might fry the decoder, so this is safety first, especially as new sound decoders can cost as much as a loco.
2 – When putting screws back, turn the head anti-clockwise first until you feel the screw drop into the already gouged thread, then tighten finger tight clockwise as normal. This avoids the screw making a new thread in the plastic which if repeated would eventually make the screw come loose or lose its bite.
I used a Massoth XLS decoder with the appropriate sound files loaded (part number 8220096) with a Massoth 70mm 2W speaker (part number 8241030).
The exploded parts diagram from LGB is useful for dismantling the loco.
http://www.onlytrains.com/manuals/2095-1.pdf
There are only four screws to remove the body (part 65 on page 3). Remember to un-clip the 4 brake hoses before removing the body shell (parts 16 and 17 on page 2).
On my model the driver was well and truly glued in place.
The 3 brass tracks along the length of the loco are for lighting. My model was light bulb lit with light tubes to carry the light to the 3 front and rear lights. Note that later models use LEDs.
All this wiring was carefully unsoldered leaving only the black and brown wires from the bulb holder in place.
Undoing the two bogie retaining screws releases the bogies.
The two wires are track power to power the lighting in DC mode. These were un-soldered and labelled should restoring the loco to original state DC be required.
The bogie was disassembled by first removing the cranks.
Then the bogie surround was un-clipped.
Wheels are moved carefully (just pull them off) making sure the brushes on springs behind the wheels are not lost.
You can leave the pickup shoes in place. Undo the fours screws and carefully lift off the top half of the power block.
Carefully lift out the motor, watching out for the little ball bearings at each end of the drive shaft. Remove the capacitor from the motor power tags, and solder 12” (30cm) wire to each tag. I used LGB colour coding, green and yellow, and 24/2 wire. I applied shrink wrap tubing to the first ¾” (2cm) to isolate the motor power tags from the track pickup. (In the aforementioned video the track supply tags were snapped off, but I wanted to retain the option to retrofit to DC). I drilled two holes, one in each shell half, to carry the power wires outside the power block. You can see where the holes run by following the yellow wire in the picture below.
The two halves can now be re-assembled, taking care that the wheels are aligned otherwise the crankshafts will be out of alignment. Insert the springs with brushes on first and push each wheel in place on top of the brush.
To hold the wheels in place before the cranks are refitted use some rubber bands, otherwise you will find the brush springs force the wheels off.
Now refit the cranks and screw them into place finger tight.
Note the wires emerge from the same end of the power block as the existing track power tags. I soldered white and brown wires to the track power tags. To test the connections in DC mode I connected white to yellow and brown to green and tried it out on a DC test track.
Repeat for the other motor block. Note that you should use the “other end” of the power block as the motors are aligned in the same direction but the wires need to emerge at the front or the back.
Both motor blocks were tested together in DC mode to make sure they would operate in the same direction. The wires emerge from the power blocks through the same holes used by the old track power cables.
I tested out the decoder, trying it on DCC programming track first. To connect the decoder I used the existing leads from the decoder and used copper wire from a stripped 3 core mains cable to simulate the standard LGB decoder socket.
I attached the speaker using the lead and plug supplied with the decoder. I used the existing brass strips to carry the power to the light bulbs. The lighting connections (orange and black) are soldered to the brass strips, orange for the live and black for the two commons (front and rear lights). I used 16/2 wire for the lighting circuit.
The complete assembly looks like this. The decoder is held in place with the two screws provided using the holes that hold the screws that fasten the weights in place. I covered the back of the decoder with insulating tape to stop it accidentally touching the metal weight. I used a spray paint tin lid as the speaker enclosure, sealing it with black sticky stuff (can’t remember the trade name for this). The body can now be replaced. Some allowance must be made for the wires trapped by the cab walls between the body and the base.
You can find a short video clip of completed loco below.
Hope this helps someone.
This model had old power blocks with only two external connections (track power). DCC requires you to intercept the track power before distributing it to the motors. The power connection from the track to the motor is handled inside the block so you have to dismantle the two power blocks and get the soldering iron out.
As I have never dismantled a power block before I did a bit of googling and I found this YouTube video from a chap called Bam Bam very helpful:
It also had two handy tips that apply to any work like this:
1 – Always try out your newly wired decoder on programming track first. If you can’t read or write a CV something is wrong, most likely a short somewhere. If you connected this straight to power you might fry the decoder, so this is safety first, especially as new sound decoders can cost as much as a loco.
2 – When putting screws back, turn the head anti-clockwise first until you feel the screw drop into the already gouged thread, then tighten finger tight clockwise as normal. This avoids the screw making a new thread in the plastic which if repeated would eventually make the screw come loose or lose its bite.
I used a Massoth XLS decoder with the appropriate sound files loaded (part number 8220096) with a Massoth 70mm 2W speaker (part number 8241030).
The exploded parts diagram from LGB is useful for dismantling the loco.
http://www.onlytrains.com/manuals/2095-1.pdf
There are only four screws to remove the body (part 65 on page 3). Remember to un-clip the 4 brake hoses before removing the body shell (parts 16 and 17 on page 2).
On my model the driver was well and truly glued in place.
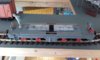
The 3 brass tracks along the length of the loco are for lighting. My model was light bulb lit with light tubes to carry the light to the 3 front and rear lights. Note that later models use LEDs.
All this wiring was carefully unsoldered leaving only the black and brown wires from the bulb holder in place.
Undoing the two bogie retaining screws releases the bogies.

The two wires are track power to power the lighting in DC mode. These were un-soldered and labelled should restoring the loco to original state DC be required.
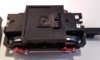
The bogie was disassembled by first removing the cranks.
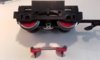
Then the bogie surround was un-clipped.
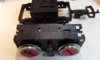
Wheels are moved carefully (just pull them off) making sure the brushes on springs behind the wheels are not lost.
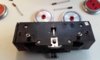
You can leave the pickup shoes in place. Undo the fours screws and carefully lift off the top half of the power block.
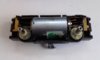
Carefully lift out the motor, watching out for the little ball bearings at each end of the drive shaft. Remove the capacitor from the motor power tags, and solder 12” (30cm) wire to each tag. I used LGB colour coding, green and yellow, and 24/2 wire. I applied shrink wrap tubing to the first ¾” (2cm) to isolate the motor power tags from the track pickup. (In the aforementioned video the track supply tags were snapped off, but I wanted to retain the option to retrofit to DC). I drilled two holes, one in each shell half, to carry the power wires outside the power block. You can see where the holes run by following the yellow wire in the picture below.
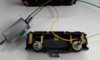
The two halves can now be re-assembled, taking care that the wheels are aligned otherwise the crankshafts will be out of alignment. Insert the springs with brushes on first and push each wheel in place on top of the brush.
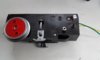
To hold the wheels in place before the cranks are refitted use some rubber bands, otherwise you will find the brush springs force the wheels off.
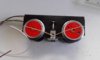
Now refit the cranks and screw them into place finger tight.
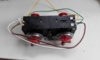
Note the wires emerge from the same end of the power block as the existing track power tags. I soldered white and brown wires to the track power tags. To test the connections in DC mode I connected white to yellow and brown to green and tried it out on a DC test track.
Repeat for the other motor block. Note that you should use the “other end” of the power block as the motors are aligned in the same direction but the wires need to emerge at the front or the back.
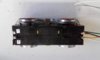
Both motor blocks were tested together in DC mode to make sure they would operate in the same direction. The wires emerge from the power blocks through the same holes used by the old track power cables.
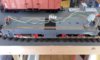
I tested out the decoder, trying it on DCC programming track first. To connect the decoder I used the existing leads from the decoder and used copper wire from a stripped 3 core mains cable to simulate the standard LGB decoder socket.
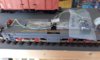
I attached the speaker using the lead and plug supplied with the decoder. I used the existing brass strips to carry the power to the light bulbs. The lighting connections (orange and black) are soldered to the brass strips, orange for the live and black for the two commons (front and rear lights). I used 16/2 wire for the lighting circuit.
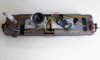
The complete assembly looks like this. The decoder is held in place with the two screws provided using the holes that hold the screws that fasten the weights in place. I covered the back of the decoder with insulating tape to stop it accidentally touching the metal weight. I used a spray paint tin lid as the speaker enclosure, sealing it with black sticky stuff (can’t remember the trade name for this). The body can now be replaced. Some allowance must be made for the wires trapped by the cab walls between the body and the base.
You can find a short video clip of completed loco below.
Hope this helps someone.