JimmyB
Now retired - trains and fishing

Hopefully the title has got your attention, here is the problem:
In my new expansion I have track coming in at different levels one raising and one dropping to meet at the same height. Having got my base (slabs) at the correct height for the lower level, the higher level has a gap between the track and base until the transition is complete. What can I use under the track, I would have thought concrete is out as the thickness (or thinness) would make it prone to cracking, so I have thought about self-levelling compound, would this hold without cracking, to is there smoother way.
The area in question is circled:
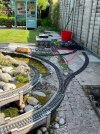
In my new expansion I have track coming in at different levels one raising and one dropping to meet at the same height. Having got my base (slabs) at the correct height for the lower level, the higher level has a gap between the track and base until the transition is complete. What can I use under the track, I would have thought concrete is out as the thickness (or thinness) would make it prone to cracking, so I have thought about self-levelling compound, would this hold without cracking, to is there smoother way.
The area in question is circled:
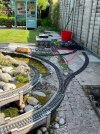