
I bought this loco for around £145 back in October 2020. I had been involved with suggesting the price to a lady that had asked us for some values and as nobody appeared to be interested I took the opportunity to buy it as I thought it looked rather nice. It is a Piko 0-6-0 Chassis with what I believe to be a GRS kit built body. Rather nicely done with a good cab interior, it was set for 2 rail pick up and ran fine though as I will relate later I was surprised it ran at all. Below you can see work under way and the shambles that is my workbench when a project is under way.
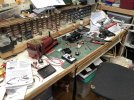
As always my intention was to convert it to Battery Operation using Fosworks kit. No fancy DCC (I do not see the worth of the loco as justifying the expense for a sound chip) so a MLS sound Unit would also be installed. But first up was to make space for the gear, battery, MLS, Rx, speed control and of course fuse and wires. Inside there was a frame top sitting just above the motor block but under this was the space for all the kit inside the boiler. So some drastic attack work with the Multi Purpose Saw got me inside the space. You can see the space made below.
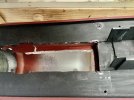
Here I have drilled and tapped the cutout using 10ba screws using some off-cut brass to hold the cutout in place, this will hold the sundry electrical bits in place. As can be seen on the left even more space had to be hacked out to get my 8aa NiMh Battery Pack to fit in.
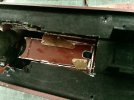
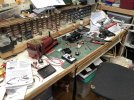
As always my intention was to convert it to Battery Operation using Fosworks kit. No fancy DCC (I do not see the worth of the loco as justifying the expense for a sound chip) so a MLS sound Unit would also be installed. But first up was to make space for the gear, battery, MLS, Rx, speed control and of course fuse and wires. Inside there was a frame top sitting just above the motor block but under this was the space for all the kit inside the boiler. So some drastic attack work with the Multi Purpose Saw got me inside the space. You can see the space made below.
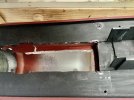
Here I have drilled and tapped the cutout using 10ba screws using some off-cut brass to hold the cutout in place, this will hold the sundry electrical bits in place. As can be seen on the left even more space had to be hacked out to get my 8aa NiMh Battery Pack to fit in.
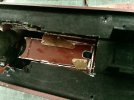
Last edited: