ge_rik
British narrow gauge (esp. Southwold and W&LLR)

A thumbs-up from me for TinkerCAD. I wanted to create some window frames for my next model building and after spending a day and half drawing fairly simple frames in SketchUp and finding repeatedly they were unprintable (as was my language!) because they were internally inconsistent, I looked around for an alternative 3D drawing package which a mere mortal such as myself could use.
TinkerCAD came to my rescue.
It's an online tool which has been designed for kids to use. OK - it doesn't have all the fancy bells and whistles of SketchUp or FreeCAD, but within an hour I had managed to draw my first window frame - and what's more, I exported it as a .stl file and it imported into my slicer software (Cura) with no problem. Within another couple of hours I had followed a couple of really great online tutorials and discovered it does actually have some clever tricks up its sleeve.
For fairly basic drawing tasks, I would thoroughly recommend it - it doesn't require a degree in computer engineering to learn how to use it.
And here are the outcomes just to prove it....
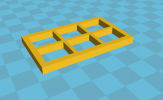
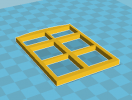
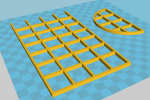
Rik
TinkerCAD came to my rescue.
It's an online tool which has been designed for kids to use. OK - it doesn't have all the fancy bells and whistles of SketchUp or FreeCAD, but within an hour I had managed to draw my first window frame - and what's more, I exported it as a .stl file and it imported into my slicer software (Cura) with no problem. Within another couple of hours I had followed a couple of really great online tutorials and discovered it does actually have some clever tricks up its sleeve.
For fairly basic drawing tasks, I would thoroughly recommend it - it doesn't require a degree in computer engineering to learn how to use it.
And here are the outcomes just to prove it....
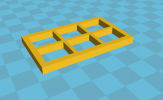
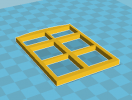
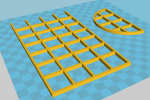
Rik