
I inherited a couple of Railcars when Andy Rush died in 2013, one a Diesel one that was Track Powered with a Massoth Sound Chip in it. Phots of this machine have appeared in the Forum before. The second was the Prototype of what was to be a short run of Overhead Electric Railcars. This was basically a Body Shell converted from a Newquida Coach and a couple of I think USA Trains Power Bogies, Roof Flat pre cut plus a GRS Roof Profile to sit on top. On the Dunnybahn it will be a Diesel Railcar and to that end I ordered last week from Steve who now has taken over from Peter Spoerer the bits that I needed. These arrived in the Post very quicky despite Steve needing to make the Battery Pack up as a special. They in fact arrived yesterday but I was out so collected the parts today.
Prior to Today I have done a little work on the beast just fitting the Bogies and making a bit of a bodge to where the Loo will be to fit one of the Bogies. One of the bogies has been adapted so that it can Swivel Left to Right and the other has been made to sit flat. These fits were done to ensure that the Railcar does not lean, a problem that we had with Andy's original one that I managed to fix after considerable bad language. The following pics attempt to show the arrangement without completely pulling things apart again.
The A End Bogie has the Brass U shape held on with the Screws at each end. This has to be done with great care as these hold Thrust Bearings in place.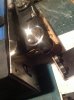
The B End has a piece of Copper Clad with the Bogie Screws being used as Pivot Points and a Screw in the Centre to hold it all in place.
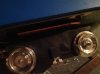
Pic below shows pretty well the Body as modified by Andy just sitting on the Bogies as fitted by me.
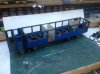
I wanted to get the Batteries into the Roof and a little work with some spare Aa's that were kicking around showed that I could fit 5x3 (well a few more actually but 15 is plenty) under the GRS Roof Profile and it would still sit flat on the Black Plastic as shown.
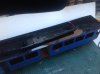
Showing the Roof Profile test fitted. Starting to look more like a Unit.
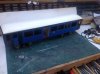
The various Power Parts shown lined up waiting to be stuffed somewhere in the body.
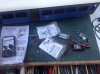
Having managed to wedge everything in it seamed like a good time for a test run. Here is the beast in the Garden during that Testing. Note the hanging on/off switch and charging plug. Plus a YouTube Vid of the run.
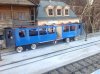
Battery was temporarily shoved into the Passenger Compartment. Viper, RC Reciever and Sound Unit stuffed into the Rest Room, was going to say Bog but I thought that would be a little uncouth.
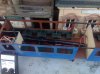
Below shows the arrangement for the Wires from the Bogies to the Electrical system. Inside the Trunking there is a Choc Block that joins the wires and two bogies together. A few holes had to be drilled to get wires in place.
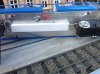
List of parts that I have used to get this beast Battery Powered:-
- Mylocosound Diesel Sound Card
- AA Battery Pack 15 cells low discharge NiMH
- No1 Loom with a Metal Toggle Switch
- OMNi Tx 2.1 Transmitter
- OMNi Rx 2 Reciever
- Viper ESC-125 Speed Controller
- 3 Way Sound Card Lead
- SND-500 50mm Speaker
All thoughtfully connected together by Steve, all I had to do was wire in the Bogies to get it all working.
I was originally with Bench Tests a little unsure about the Viper as it appeard to want to shoot off in what appeard to be an uncontrolled way. But test running on Rails showed it to be a positive and controllable, more than adequate for a bit of Shunting when handling Mixed Trains.
So thus far I am pleasd with my efforts today to get this to a rolling unit. Next up will be to get on with the detailing and not least Windows.
Prior to Today I have done a little work on the beast just fitting the Bogies and making a bit of a bodge to where the Loo will be to fit one of the Bogies. One of the bogies has been adapted so that it can Swivel Left to Right and the other has been made to sit flat. These fits were done to ensure that the Railcar does not lean, a problem that we had with Andy's original one that I managed to fix after considerable bad language. The following pics attempt to show the arrangement without completely pulling things apart again.
The A End Bogie has the Brass U shape held on with the Screws at each end. This has to be done with great care as these hold Thrust Bearings in place.
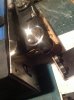
The B End has a piece of Copper Clad with the Bogie Screws being used as Pivot Points and a Screw in the Centre to hold it all in place.
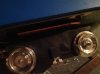
Pic below shows pretty well the Body as modified by Andy just sitting on the Bogies as fitted by me.
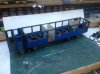
I wanted to get the Batteries into the Roof and a little work with some spare Aa's that were kicking around showed that I could fit 5x3 (well a few more actually but 15 is plenty) under the GRS Roof Profile and it would still sit flat on the Black Plastic as shown.
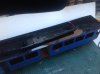
Showing the Roof Profile test fitted. Starting to look more like a Unit.
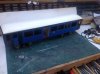
The various Power Parts shown lined up waiting to be stuffed somewhere in the body.
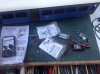
Having managed to wedge everything in it seamed like a good time for a test run. Here is the beast in the Garden during that Testing. Note the hanging on/off switch and charging plug. Plus a YouTube Vid of the run.
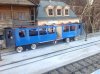
Battery was temporarily shoved into the Passenger Compartment. Viper, RC Reciever and Sound Unit stuffed into the Rest Room, was going to say Bog but I thought that would be a little uncouth.
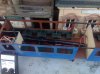
Below shows the arrangement for the Wires from the Bogies to the Electrical system. Inside the Trunking there is a Choc Block that joins the wires and two bogies together. A few holes had to be drilled to get wires in place.
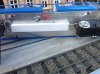
List of parts that I have used to get this beast Battery Powered:-
- Mylocosound Diesel Sound Card
- AA Battery Pack 15 cells low discharge NiMH
- No1 Loom with a Metal Toggle Switch
- OMNi Tx 2.1 Transmitter
- OMNi Rx 2 Reciever
- Viper ESC-125 Speed Controller
- 3 Way Sound Card Lead
- SND-500 50mm Speaker
All thoughtfully connected together by Steve, all I had to do was wire in the Bogies to get it all working.
I was originally with Bench Tests a little unsure about the Viper as it appeard to want to shoot off in what appeard to be an uncontrolled way. But test running on Rails showed it to be a positive and controllable, more than adequate for a bit of Shunting when handling Mixed Trains.
So thus far I am pleasd with my efforts today to get this to a rolling unit. Next up will be to get on with the detailing and not least Windows.
Last edited: