I suggested the direct burial wire as an option. But I pretty much agree with Alan (Stockers). I'm using mains wire (as the Brits call it). But new, not used. 500ft of single conductor 12 AWG stranded was around $40 at Home Depot. I use black, white, green and red for power feeds. This is buried directly under the blocks or in the ballast supporting my rails. The following pics show how I made up my buss wire and feeders.
Pic 1 shows the label for the wire I used. I use the wire in pairs. 2 is how I rigged the wire reels for easy feeding. This was inspired by the electricians at work and their wire cart. The setup makes it easy to pull off long lengths of wire without it twisting into a mess.
1
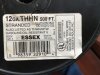
2
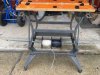
3
I pull the wire in pairs to have equal lengths of 30 to 40 meters. 3. Next, one end of the paired wires is chucked in a drill using a screw-eye and a cable-tie. The other end is similarly attached to something solid and unmovable. Stretch out the wire and run the drill. This will make a "twisted pair".
4. Prep the twisted pair for attaching track feed leaders. I stripped about 1 cm of insulation from the buss wires at 2 meter intervals. The feeders are 50cm lengths of LGB 51233 cable. All the feeders were prepped ahead of time with crimp on eyes on one end and about 2 cm of insulation stripped from the other end. The bare ends of the feeder are wrapped around the stripped area of the buss wires as shown in 4 & 5. A paste flux was worked into the wire joint and the joints soldered one at a time. 6. A 200w soldering iron is clamped in my Workmate making only two hands necessary. The iron is loaded with solder and the fluxed joint is brought to the iron. The solder gets sucked up into the joint.
4
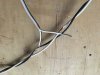
5

6
7. After all the joints were soldered each was given two coats of "Liquid Electrical Tape". The first coat at the beginning joint was cured enough for the second coat by the time I got to last joint on the cable. A cable tie as shown in pic 5 acts as a strain-relief at each feeder once the liquid tape had cured for a few hours. 8. shows a finished feeder. It takes me about 4 hours to finish a 40 meter buss/feeder wire.
7
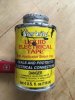
8
The crimped on eyes connect to the rails at the screws that secure Split-Jaw track clamps. The length of the feeders assures each will reach a set of track clamps even when using flex-track.
Phil S.