GAP
G Scale Model Trains, 1:1 Sugar Cane Trains

I saw this project on Trainelectronics by Dave Bodnar Simple Servo Controller
Having one of the servo testers and some servos I decided to see if I could adapt it to my outside layout.
I have made a mock up of the controller and after a bit of experimenting in the shed with a test bed I put 2 servos out on the layout next to 1 set of LGB points and 1 set of Aristocraft points to see how they will go when I run a train through them.
If successful I will convert all my points to servo control.
I plan to put the controllers into a weatherproof enclosure and put a signal box over the top to disguise it.
My biggest worry was that the distance between the points I want to control and the controllers might be too large and the signal would degrade.
I made a 12 Ft long test cable and successfully changed a set of points over that distance.
As I have 2 signal boxes I will split the 12 sets of points I have into groups of 2 (6 controllers in each signal box).
The control switches will be weatherproof ones and mounted in enclosures with a lid.
Edit;
As the servo tester has outputs to control 3 servos at the same time, I have come up with the idea of using a second servo to move a semaphore signal so I can see which way the points are set at a glance.
I tested the idea on my bench set up and the second servo moved in time with the point driver.
Pictures of my test set up.
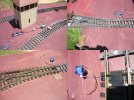
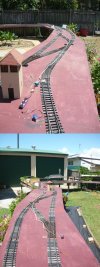
Having one of the servo testers and some servos I decided to see if I could adapt it to my outside layout.
I have made a mock up of the controller and after a bit of experimenting in the shed with a test bed I put 2 servos out on the layout next to 1 set of LGB points and 1 set of Aristocraft points to see how they will go when I run a train through them.
If successful I will convert all my points to servo control.
I plan to put the controllers into a weatherproof enclosure and put a signal box over the top to disguise it.
My biggest worry was that the distance between the points I want to control and the controllers might be too large and the signal would degrade.
I made a 12 Ft long test cable and successfully changed a set of points over that distance.
As I have 2 signal boxes I will split the 12 sets of points I have into groups of 2 (6 controllers in each signal box).
The control switches will be weatherproof ones and mounted in enclosures with a lid.
Edit;
As the servo tester has outputs to control 3 servos at the same time, I have come up with the idea of using a second servo to move a semaphore signal so I can see which way the points are set at a glance.
I tested the idea on my bench set up and the second servo moved in time with the point driver.
Pictures of my test set up.
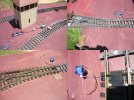
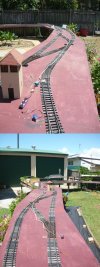
Last edited: