I installed one servo tester, wired it up to the 5V the bus and mounted a switch to the control panel.
Next I installed a servo next to a point and connected it to the tester.
Following that I connected the servo horn to the point throwbar via a control rod with a clevis pin at one end, on the other end of the control rod at the horn I put a "Linkage Stopper" (these are used by the model aircraft people quite extensively).
The stopper has a grub screw adjustment so when I set the servo travel extremities using the 2 pots I could make fine adjustments to relieve any residual tension being applied to the control rod.
As the point I started with was on a crossover, I attached another servo to the other point and connected it to one of the tester outputs (there are 3) and now both points change at the same time controlled from the one control panel switch.
Now that I have it all working I will proceed with installing the rest of the servos to my points (12 of them)
The servos I am using are waterproof and are mounted under the baseboard.
I ran my irrigation sprays that are under the baseboard and no sign of any part being wet.
We also had 4 days of heavy rain and no water got under the baseboard everything was dry.
I am going to put a smear of silicone grease around the servo shaft to increase water repellence around its entry point.
I am using double walled heatshrink with a glue inside to keep moisture out of wiring joints.
Picture of the control rod showing the clevis pin and the linkage stopper.
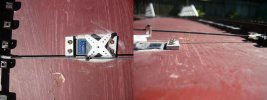