penylanpip
Registered

Like wot James said above, I purchased this little tin from Squires when proprietor Roger couldn't have been long out of nappies.
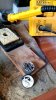
This is it after 20-odd years of soldering lots of '0' gauge wagon kits and another 10 since.
It will do all you are looking for, Jon, and the exact same item is still available on their website (bottom of page 234).... http://www.squirestools.com/files/12-17.pdf
Although there is a minimum order of £15, I bet you will find other useful kit amongst all those pages!
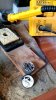
This is it after 20-odd years of soldering lots of '0' gauge wagon kits and another 10 since.
It will do all you are looking for, Jon, and the exact same item is still available on their website (bottom of page 234).... http://www.squirestools.com/files/12-17.pdf
Although there is a minimum order of £15, I bet you will find other useful kit amongst all those pages!