Small update:
I achieve what i wanted today, some real needed measurements.
And i am going to change the driving power, the motors are going to be in the tender for the electric variant.
It will give me some more benefits:
More motors is more power and i can make the tender more heavy for more traction thus more cars to haul. and if that is not enough i can with the same diameter wheel add more motors in a car further down the train as a "helper" same dia in wheels!
Simpler design and to work with.
But the mechanics where working as i would like, giving me that 2mm clearance i wanted! so i can make the wheel gauge a bit more realistic instead of 41mm to 43mm instead of the 45mm i would really like, but hey tis is a big loco...
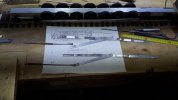
So this one went oke
But for the much needed cylinders measurement/dimensions i had to do something........
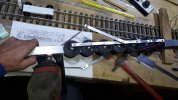
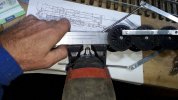
Believe it, it did not fit, so i had to "hover" the jigsaw above the frame and wheels to cut it...good luck if you want to try this and dont have enough experience with a jig saw..
I did not toke the frame apart, i just cut it with everything in place....
On the bench is a 4 meter in radii track.
The basic mechanics worked like they should work, oke not a Swiss clockwork, but what had to be done was done properly.
And i have finally some needed measurements, oke must be fine tuned...
But it drove happy back and forward, several times, with cranking up the speed i had to put some weight on the frame.
I am no photo hero, but i got what i wanted...A lot of answers to a lot of problems, lets make a AA20 4.0!(please keep in mind that live steam is the end goal, this is just play/experimenting).
I can make a groceries list for a month for a 6 person family of things that must be improved....
I will get there with a accurate and good working AA20
With best regards and thanks for reading, Igor