Small update on what i was doing.
With the inspiration of Stavers, i made some turn outs, with the help of templot2, marveles program! there is a big learning curve, but i will get the hang of it.
The frog casting was a moderate success, however one mold would be for one turn out model.
The alloy i used was off my bhn scale: bigger than 50 bhn, with no water drop or heat treatment, after air cure i think a end bhn of 65-70!
Harder than alu.
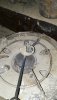
Melting alloy
So....Casting worked, but not for the whole idea.
With templot i printed a turnout and start to make a mold for the turn out:
The first one was not a success, i used the parts for the second one, no need to be educated: it was no success either.
Third one is in the mold, i spend some more time with the tongs, to make them shift track.
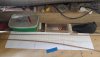
I tried first with aluminium strips 5x7mm, they broke, wood was very good
I did not make a lot of pictures, but i think the idea is clear.
I made several jigs to easy up the work on the sleepers/ties for the turnouts, crossings, strait, ect.
The third turnout has modification tongs:
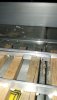
I think i will go with that one. The tongs need to be a little higher, that will come with the mechanics involved.
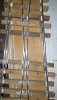
Scrambled up all the pictures...above pic is the second turnout, with the materials from the first turnout.
I am no camara hero, just took the pictures with my phone.
So that was i was up to the last couple of days, in a hasty pase, work is demanding a lot of time in the moment, sorry for the chaotic mess and a not clear line in the story.
Things need to be changed and improved: sharp new fresh sawblades at 2.0mm for the tablesaw and the cutter saw for this purpose.
Work with the putty above 15C!
I think i figured out the clearance between the rail and the safety rail(frog included) 4mm.
Wood (fresh oak was used, fir i only got that in trees's for firewood, i dont like the grain but i will try)needs a protective layer: woodstain.
Any thought idea hint tip or trick is as always welcome.