justme igor
Registered

progress on the 5way....
I toke my arbore press into the shed to make it myself easy:
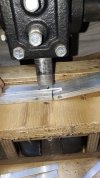
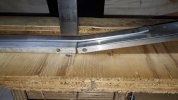
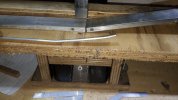
I "reconfigured"my jigsaw stand for the long points, jeezzz they are really a pain in my...let keep it polite...
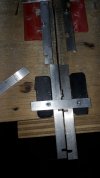
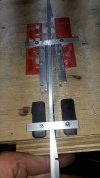
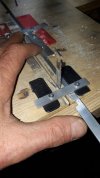
Must still work on this principal with the jig saw, it is not really to my satisfaction yet.
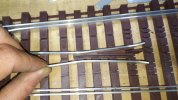
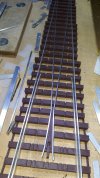
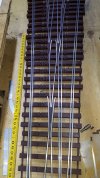
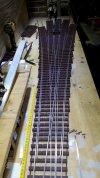
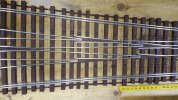
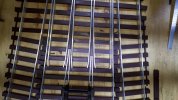
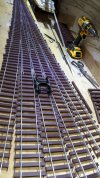
The boogie you see is my testing boogie, it is exact 44mm (all my boogies are 44mm btw) from flange to flange and the gauge is 45mm,.
So i have 0.5mm clearance between each flange and rail times 32 = to big to get it prototypical correct = 1.6 cm = 0.6 cm in proto to big
Smooth running so far.
So i changed the frogs for the 6th time (look at my other projects) for better looking/appearance better running better building and more firm
Next week i hope i have the time to create the points/switch blades.
Yes this is one sweet but tough cookie with a bonus on learning experience.
Practice makes better.
Some stats:
1.5 kilo abs.
~70 hours printing
And so far 17.50 meters of aluminium strip is in it.
Thanks for reading, with best regards Igor
I toke my arbore press into the shed to make it myself easy:
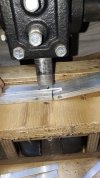
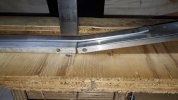
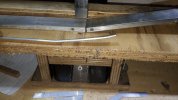
I "reconfigured"my jigsaw stand for the long points, jeezzz they are really a pain in my...let keep it polite...
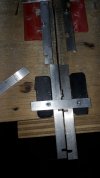
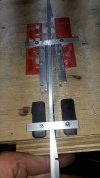
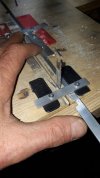
Must still work on this principal with the jig saw, it is not really to my satisfaction yet.
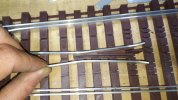
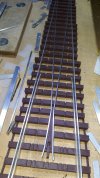
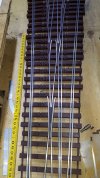
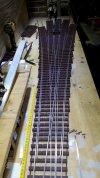
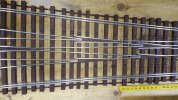
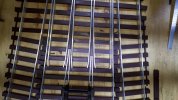
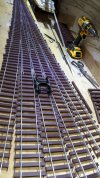
The boogie you see is my testing boogie, it is exact 44mm (all my boogies are 44mm btw) from flange to flange and the gauge is 45mm,.
So i have 0.5mm clearance between each flange and rail times 32 = to big to get it prototypical correct = 1.6 cm = 0.6 cm in proto to big

Smooth running so far.
So i changed the frogs for the 6th time (look at my other projects) for better looking/appearance better running better building and more firm
Next week i hope i have the time to create the points/switch blades.
Yes this is one sweet but tough cookie with a bonus on learning experience.
Practice makes better.
Some stats:
1.5 kilo abs.
~70 hours printing
And so far 17.50 meters of aluminium strip is in it.
Thanks for reading, with best regards Igor